塗装治具によるコスト削減戦略:工程短縮と塗料ロス削減を実現するために


- ∨ 塗装治具とは?
- ∨ 治具が担う3つの重要な役割
- ∨ 塗装方法に合わせた代表的な治具の種類と特徴
- ∨ 塗装治具が原因で起こる「塗料の無駄」
- ∨ 塗着効率を上げる基本的な方法
- ∨ 塗装治具メンテナンスの基本
- ∨ 革新的な剥離技術:熱文化意識塗膜剥離炉
塗装治具によるコスト削減戦略:工程短縮と塗料ロス削減を実現するために
塗装治具とは?
塗装現場における塗装治具は、オールマイティーに使用できるものではなく、ワークや塗装方法にあわせてオリジナルで作成するものです。
お客様毎の「知恵と工夫の塊」と言える塗装治具は、生産効率とコスト削減に直結する重要な役割を担っています。
治具が担う3つの重要な役割
塗装治具には3つの基本的な役割があり、これらを理解することが最適化への第1歩です。
1. 塗装ワークの固定
ワークが不安定な状態では、霧化エアーの勢いや搬送時の振動でワークが動いたり落下したりします。また、塗りたての塗料が擦れることで跡が残り、塗装不良の原因となります。
確実な固定によってこれらの問題を防止できます
2. 塗装ワークの搬送
前処理、除塵、塗装、乾燥などの各工程間で、ワークに直接触れることなく搬送するためには塗装治具が不可欠です。
3. マスキング用途
塗装してはいけない箇所への塗料付着を防ぐために「固定+マスキング」の複合機能をもつ治具が活用されます。特にネジ穴などはハンガーフックで固定しながらマスキングするのが一般的です。
塗装方法に合わせた代表的な治具の種類と特徴
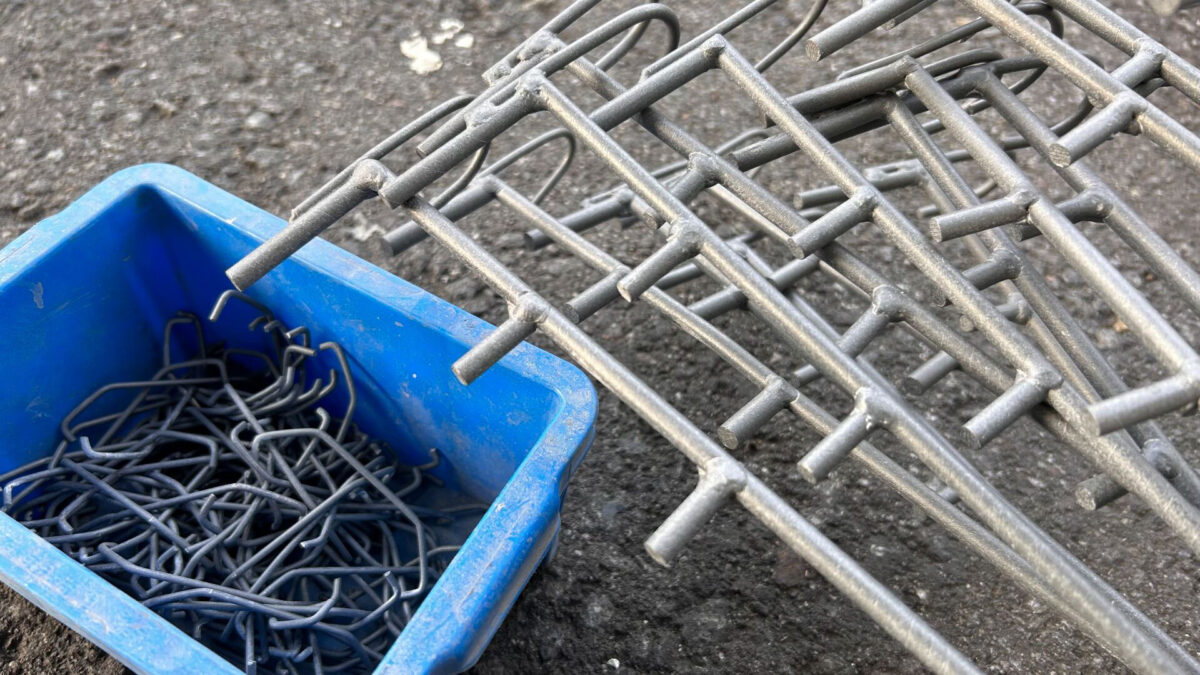
1. ハンガー式・フック式
静電塗装やバッチ塗装に用いられます。
中型の金蔵製品塗装に適しており、吊り掛けて固定します。
そのため一度に様々な方向からの塗装が可能なことが利点です。
アースを取ることにより静電塗装でも使用が可能です。
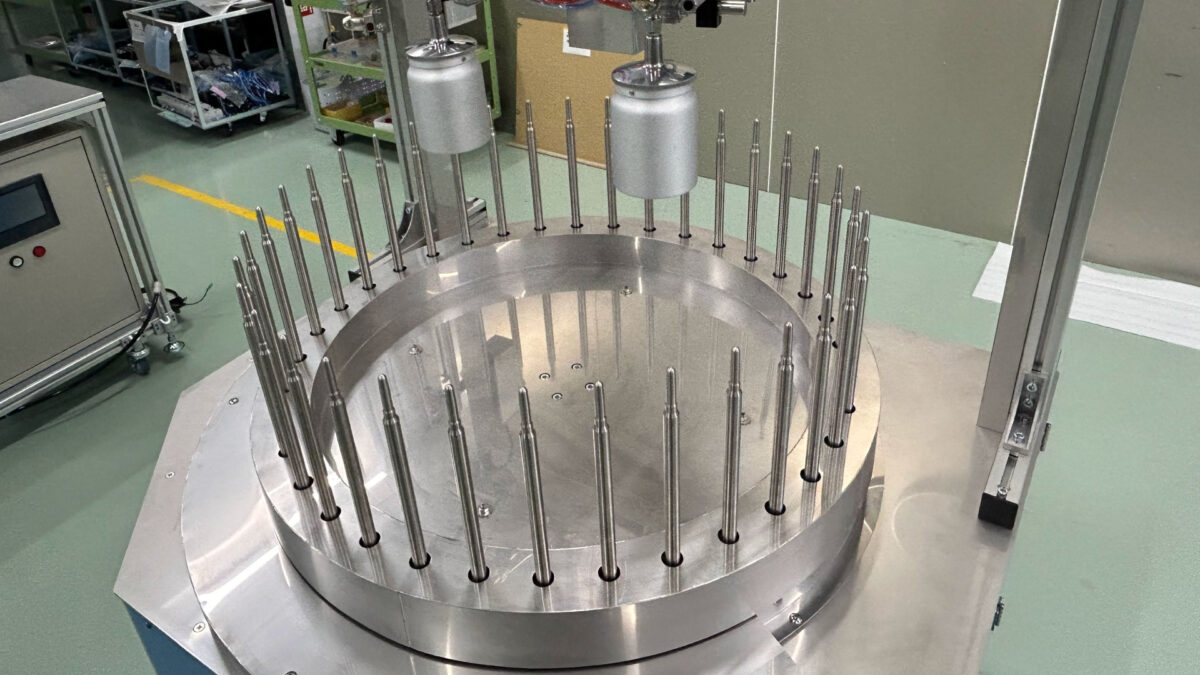
2. 固定治具
スピンドル塗装、バッチ塗装に用いられ、主にプラスチック塗装などの小型で外観品質を重視する製品に適用されます。
マスキング機能と組み合わせた治具も存在します。
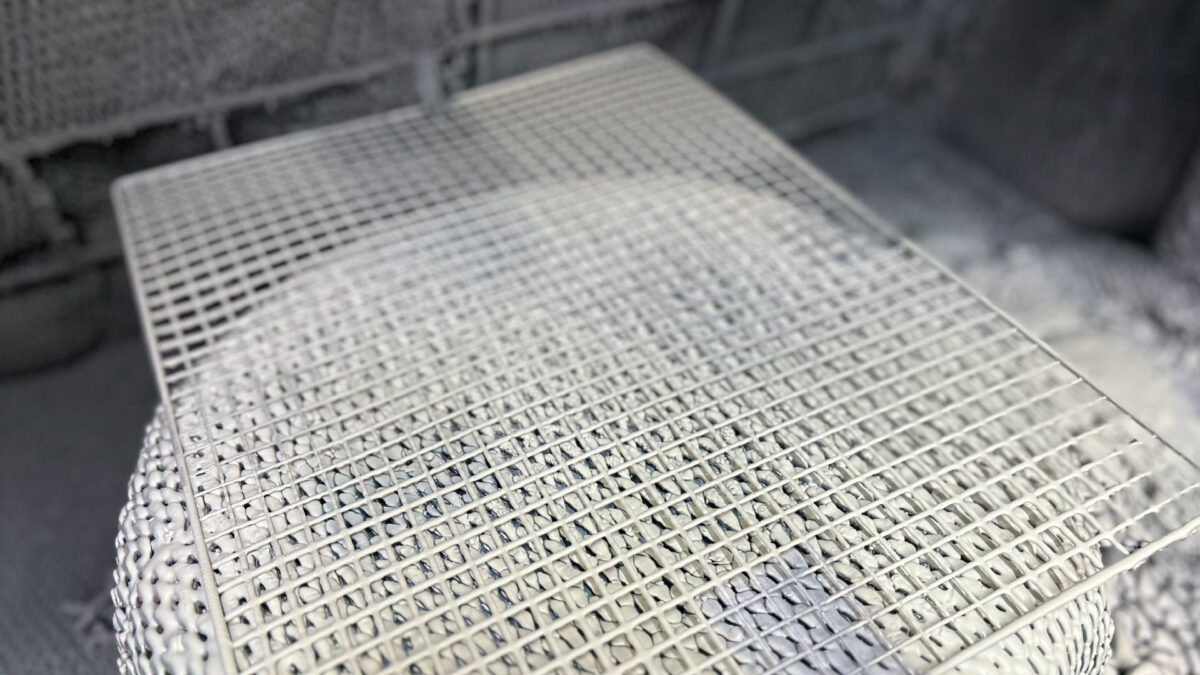
3. 塗装網
小物類の塗装に用いられます。
汎用性の高い治具ですが、アースが取りにくいため静電塗装には向きません。
以上をふまえつつ、最適な治具を選ぶためには以下の要素を考慮しましょう。
- ワークの外観を重視する面と重視しない面
- 塗装の方式(搬送方法や静電の有無)
- 生産数量
塗装治具が原因で起こる「塗料の無駄」
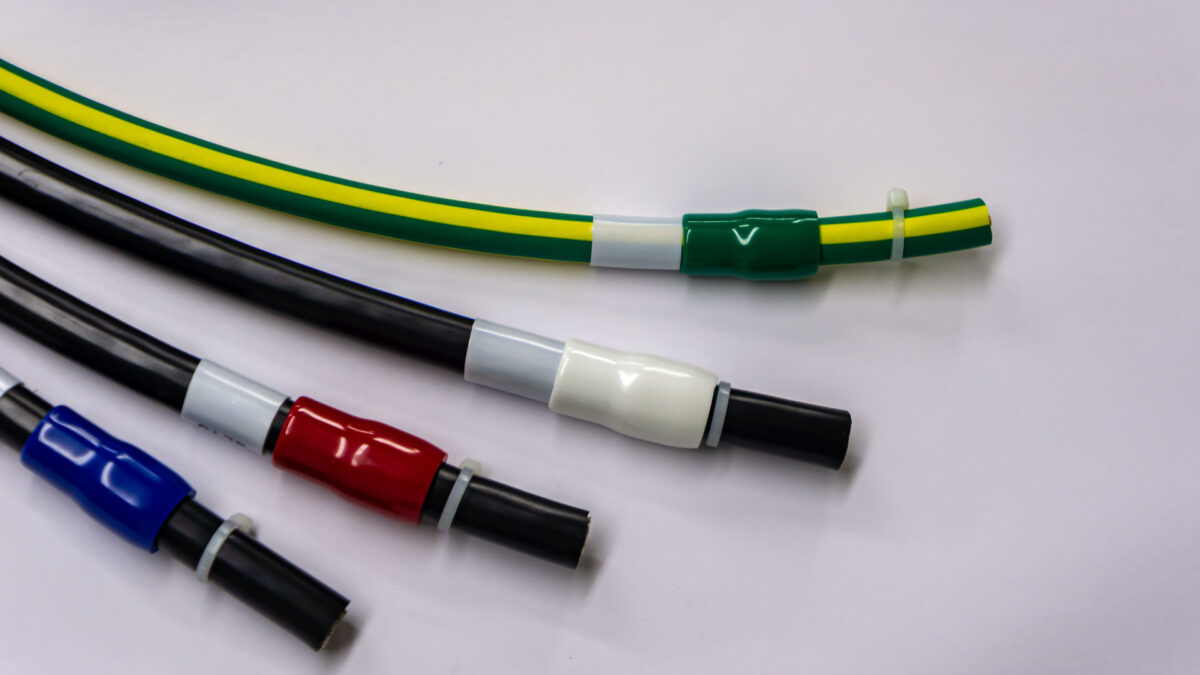
1. 塗料付着量の低下
静電塗装において、治具のアース不良は塗料付着量の大幅な低下を招きます。
対策としては、塗料の付着が原因でアースが取れなくなり、塗装が薄くなるようなことがないよう、こまめな治具の剥離作業の実施が重要です。
また1次治具、2次治具、コンベアフック等すべてのアース確認が必要です。
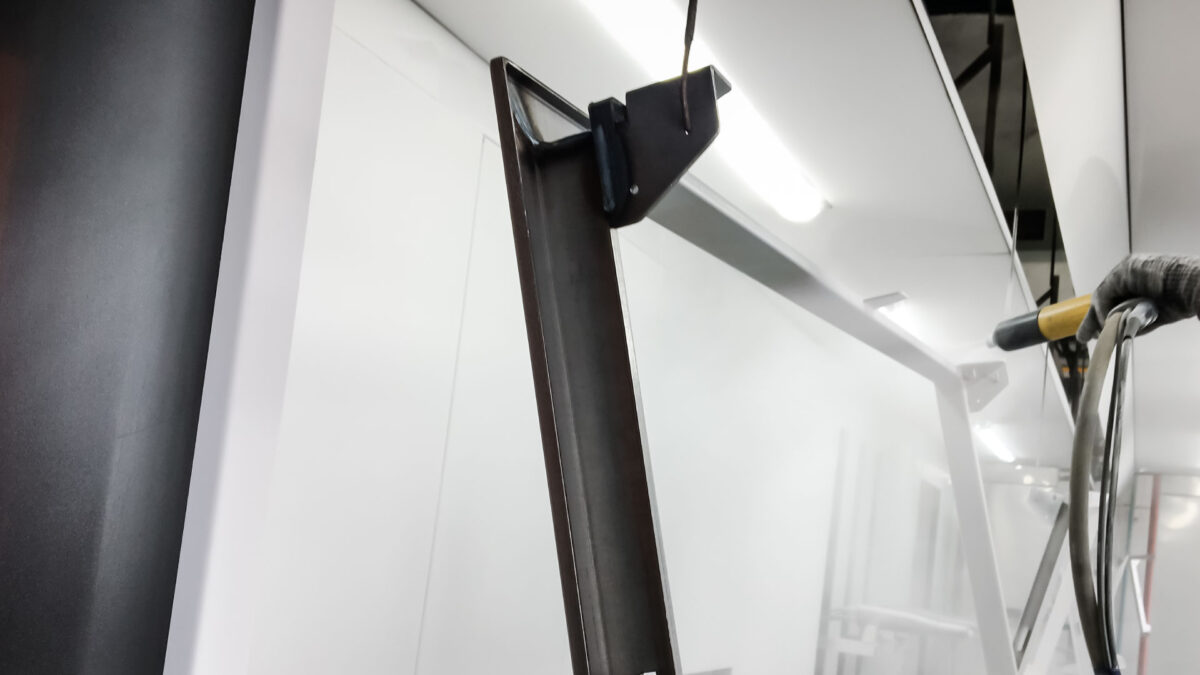
2. 塗料の無駄吹き
【治具の歯抜け】
ハンガー治具のフックが破損した状態での塗装作業継続は、深刻な塗料の無駄やロスを引き起こします。
取替可能な塗装治具への迅速な交換が必要です。
【形状の問題】
ワーク同士の間隔が不適切な場合や塗装範囲に対して治具のサイズが合っていない場合も、必要な部分に塗料が付着せずロスになります。
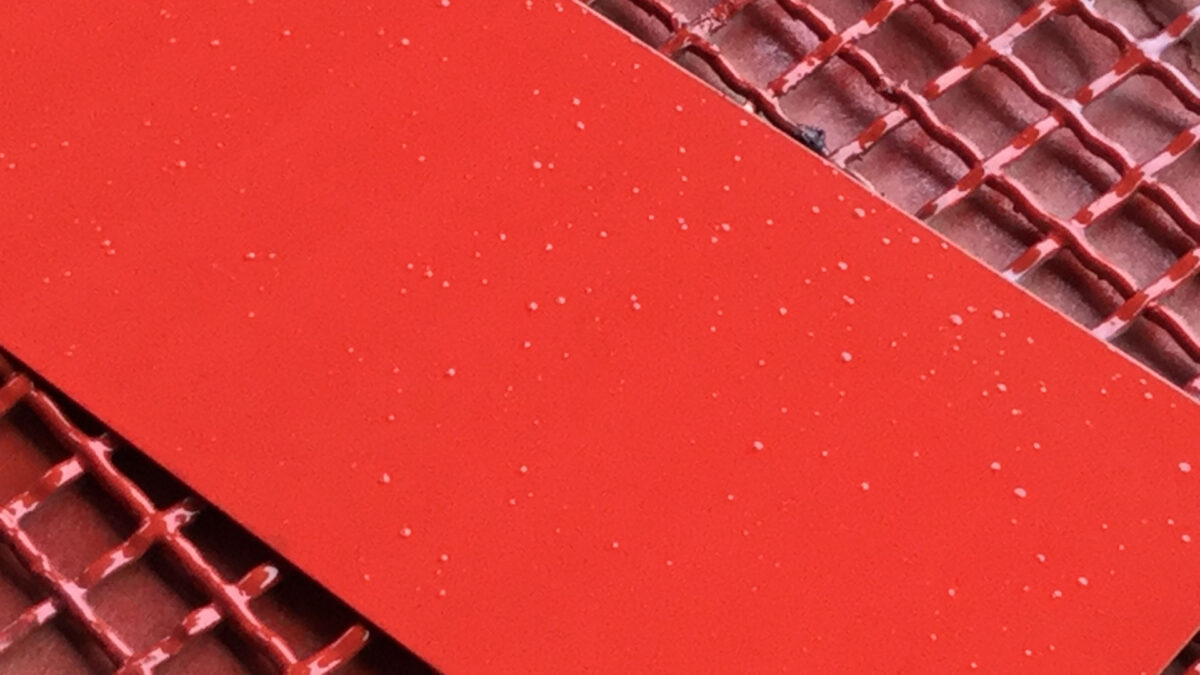
3. 塗装不良の発生
【塗装治具からのゴミ・ブツ】
塗装治具に付着した塗料ミストが固着し、振動により落下してワークに付着することで塗装不良が発生します。
この問題は定期的なメンテナンスで防止可能です。
【ワークの吊り方による問題】
静電塗装では突起部に塗料が多く付着するため、タレなどの不良が発生しやすくなります。
突起物が目立たないように引っかける、あるいは塗料を逃がすために治具に意図的な突起を設けるなどの対策が有効です。
塗着効率を上げる基本的な方法
1. 隙間なくスプレー範囲に並べる
ワーク間の隙間は塗料粒子の無駄を生みます。
可能な限り間隔をつめて配置し、複数箇所で固定することでワーク同士の間隔を保ちます。
2. 影になる箇所の対策
立体的な形状のワークでは影ができ、塗料が到達しない箇所が発生します。
一般的に「ワークの高さの約3倍程度」の間隔を空けることで防止することが可能です。
3. スプレーガン距離の統一
スプレーガン距離の差によって塗膜の仕上がりが変わり外観不良の原因となります。
ゆず肌などの凸凹にならないよう、すべてのワークを同一距離に配置することが重要です。
4. 効果的な塗装工程(少ない反転のみでの塗装)設定
塗装面数が増えると、塗装作業に時間がかかり生産効率が下がります。
反転(網返し)回数を最小限に抑えることで、作業時間の短縮と塗料消費の削減を同時に実現できます。
塗装治具メンテナンスの基本
塗装治具メンテナンスの原則は「綺麗な状態の維持」です。
主なメンテナンス方法は以下の2つです。
1. 壊れた箇所はそのままにしない
「すぐに修理」が基本です。
「知恵と工夫の塊」である治具の修理が困難な場合は、汎用品と脱着可能なアタッチメントを組み合わせた設計を採用することで、メンテナンス性を向上させることができます。
2. 小まめな剥離作業の徹底
塗膜の剥離は最も重要なメンテナンス作業です。
「溶剤剥離」や「ブラスト乖離」といった剥離方法がありますが、いずれも以下の課題があります。
・委託先の選定が困難
・最適な剥離方法の判断が困難
・剥離作業中の治具不足
・治具の破損や変形リスク
・時間やコスト、環境負荷の面
革新的な剥離技術:熱文化意識塗膜剥離炉
上記の課題を解決するために、NCCはアメリカ ポリューション社の「熱分解式塗膜剥離炉」を提案しています。
これは熱分解生後(パイロリシスTM)方式により、塗膜に熱を与えて有機物をガス化し、無機物(灰)にするものです。
ボタン一つで最先端技術による塗膜剥離が可能になり、剥離業者での効率化はもちろん、剥離の内製化を検討する企業にとっても、高品質で安定した剥離作業を実現することができます。
熱分解式塗膜剥離炉の詳細はこちらからご覧いただけます。
現場の見直しから始まり、段階的な改善を積み重ねることで、塗装治具から塗装工程全体の最適化を実現してコスト削減のための改善方法を得ることができるはずです。
ご興味のある方、剥離についてのご相談がある方は私たちにお任せください。
- ホーム
- コーティングNEWS
- 塗装部門の強み -Coating Support-
- お悩み解決・お役立ちサービス
- NCCの塗料調色サービス
- NCCオリジナル商品
- イチ押し!商品
- SDGs・エコ対策品特集
- 知って得する!豆知識
- 導入・施工事例
- └有機溶剤業務で欠かせない局所排気装置導入事例
- └NCCオリジナル自動塗装機「NEO Easy Coater フラット」導入事例
- └ゴミ・異物の発生を極限まで抑えた塗装室導入事例
- └ダクト臭気対策工事事例
- └旭サナック製粉体塗装ブース・静電粉体ハンドガンユニット「EcoDual」導入事例
- └PCP社製熱分解式剥離炉導入事例
- └(特)洗浄用シンナー導入事例
- └「3in1マルチ・ドライフィルター®」導入事例
- └粉体塗料用レシプロ自動塗装機導入事例
- └NCCオリジナル「工業用 電気式焼付乾燥炉」導入事例
- └水洗塗装ブース導入事例
- └水洗塗装ブーススラッジ処理剤「SK-GO」導入事例
- └「成形品用高密度除電処理システム」デモ事例
- └デュアル電界方式粉体ハンドガン「EcoDual」導入事例
- └「希釈用シンナー」切り替え事例
- └高塗着効率「エアミックスガン」導入事例
- └量産向け「XY塗装機」導入事例
- └「粉体塗装コンベアーライン設備」導入事例
- └米国PCP社製「熱分解式剥離炉」導入事例
- └「水洗ブース粉体塗料スラッジ浮上剤」導入事例
- └「排熱循環乾燥炉(間接加熱式)」導入事例
- └「大型・小型塗装設備・粉体塗装設備」導入事例
- └「ホコリが入らないオリジナル塗装ライン」導入事例
- └塗装ブース排気ファンの「プロによる清掃サービス」実施事例
- └「塗装治具の剥離外注化」事例
- └「塗板作成用XZ塗装機」導入事例
- └「粉体静電ガンシステム」導入事例
- └乾燥炉バーナー「着火不良点検・メンテナンス」事例
- └プラから紙へ「梱包資材」切替事例
- └エアミックスガン塗装デモ事例
- └NCCオリジナル「XY塗装機」導入事例
- └IoT機能付き電気乾燥炉導入事例
- └「熱風循環式乾燥炉」導入事例
- └「温風低圧塗装機」導入事例
- └「流動浸漬式粉体塗装機」導入事例
- └「塗装ブース維持管理支援パッケージ」導入事例
- └「塗装ブース事故防止+スポットクーラーダクト」工事事例
- └「反転機構付きXY塗装装置」導入事例
- └「レシプロ塗装機」更新事例
- └「ブロアエアーシステム」デモ事例
- └遮熱シート「キープサーモウォール」導入事例
- └「KNK溶剤再生装置」導入事例
- お客様の声
- お問い合わせ
- メルマガ申し込み
- 会社情報
- プライバシーポリシー